Usinage précis, d’excellente qualité et amélioré grâce au CoroMill MH20 de Sandvik Coromant
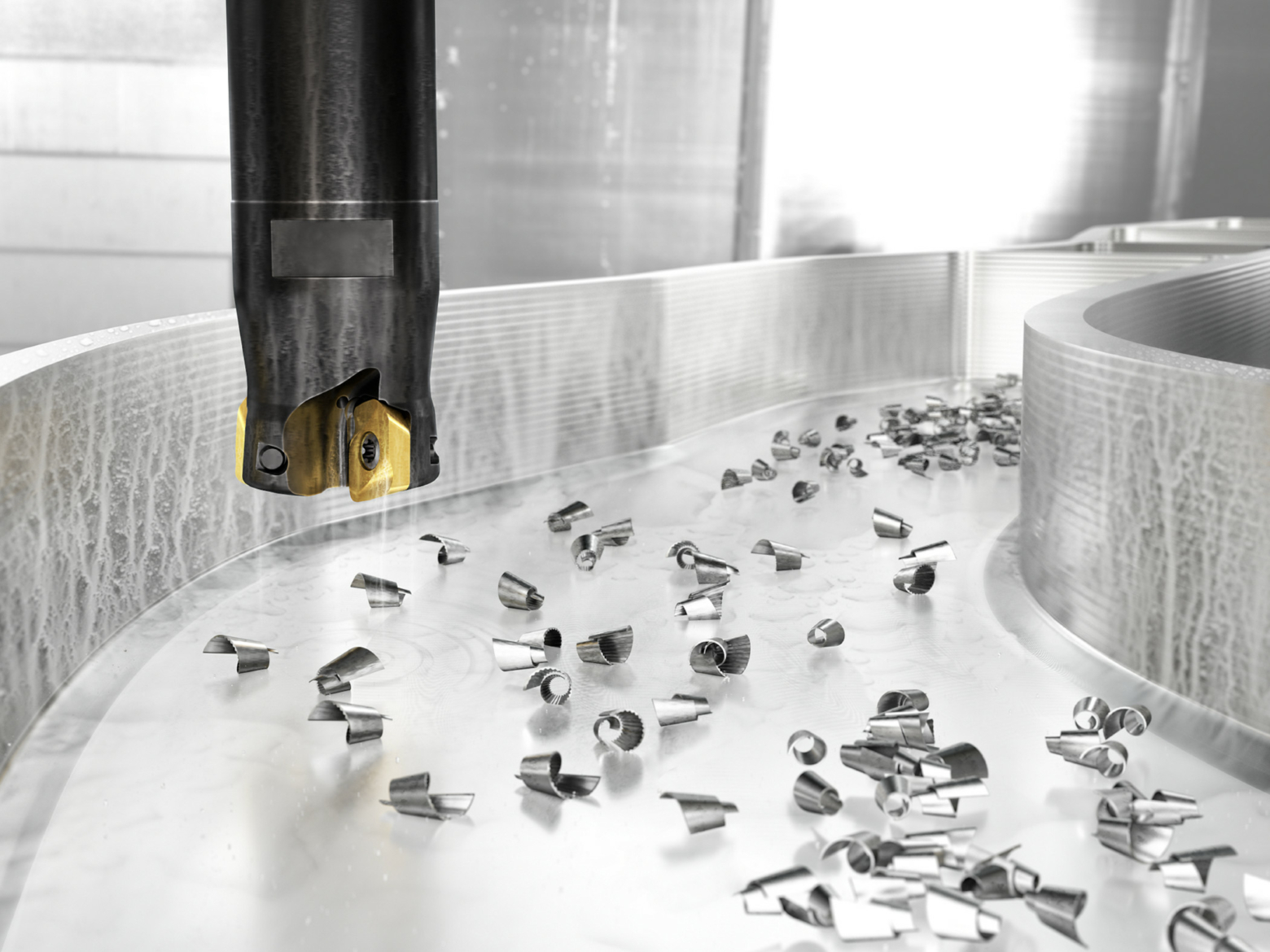
« Pour rester compétitives, poursuit le rapport de PwC, les organisations doivent pouvoir intégrer de nouveaux modèles commerciaux et de nouvelles technologies pour accélérer et s’adapter. » Pour les ateliers, l’adaptation implique de diversifier l’offre de produits et de se tenir prêts à satisfaire la demande des clients de nouveaux marchés.
Elles ont également l’obligation de détecter et d’éliminer les défauts des produits via un contrôle des erreurs. C’est un défi infini, puisque la diversification vers de nouveaux secteurs implique de manipuler des pièces à usiner fabriquées à partir d’un plus grand nombre de matériaux, comme l’aluminium et les superalliages résistants à la chaleur (HRSA). Les propriétés de dureté de ces matériaux diffèrent énormément de celles du spectre des autres. Les processus et les conditions d’usinage varient aussi beaucoup d’une pièce à l’autre. Cela comprend tout, du dégrossissage à la finition sur des pièces excentrées ou à la forme quasi définitive, coulées ou forgées.
Certains types d’usinage présentent aussi des contraintes hors du commun. Par exemple, quand un outil à grand porte-à-faux est utilisé pour fraiser des poches profondes et étroites, l’ensemble de l’installation devient instable. Cela peut rendre l’usinage imprévisible et présenter plus de risques de vibrations qui, comme nous le verrons, peuvent provoquer des défaillances de l’outil et des temps d’arrêt.
Alors que les fabricants ont besoin de solutions d’outillage garantissant un usinage sécurisé et prévisible, avec de plus forts taux d’enlèvement de métal, des cycles de plus courte durée et des changements rapides de lots de production. Heureusement, il existe une solution. Pour reprendre les termes du rapport Fabrication industrielle de PwC, « la perturbation offre une occasion d’innover. »
Mauvaises vibrations
Pourquoi ces innovations sont nécessaires ? Les vibrations d’usinage constituent un facteur à surmonter, qui affecte négativement les performances de différentes manières, dont le déplacement de l’outil et les imperfections des pièces. Elles peuvent aussi provoquer des ruptures d’outils et des temps d’arrêt imprévus. Les vibrations posent aussi le problème de la formation et du retrait de copeaux, qui sont un problème de base indissociable de l’usinage et qui réduisent l’efficacité des outils de coupe.
Un autre facteur de la sous-performance réside dans le fait que beaucoup de plaquettes présentent quatre bords. La présence de ces quatre bords se justifie par le fait que, quand un bord s’émousse ou s’ébrèche, il est facile de faire tourner ou de remplacer la pointe. Cependant, les angles des plaquettes, entre les bords plats, constituent leur partie la plus fragile. Ces bords radiaux sont conçus différemment des bords plats de la plaquette. Ils se trouvent souvent dans la zone coupante et, par conséquent, se cassent fréquemment en premier.
Tels sont les problèmes auxquels les spécialistes de Sandvik Coromant sont restés attentifs pendant la conception d’un outil nouvelle génération voué à répondre aux exigences contraignantes de nombreux secteurs. Il était fondamental que cette invention réduise le nombre d’outils, de changements et de maniements d’outils requis pendant l’usinage, pour moins de temps d’arrêt et de plus grands avantages économiques.
Le résultat est CoroMill® MH20, un nouvel outil pour le fraisage à grande avance conçu pour fraiser des cavités ou des poches constitués de matériaux ISO S, M et P.
Une occasion d’innover
Le design du CoroMill® MH20 présente plusieurs innovations. Parmi elles, un nouveau matériau pour le corps de fraise, utilisé pour les corps des queues cylindriques, qui offre un niveau de rigidité jamais vu avant sur ce type d’outil. Ce matériau minimise l’usure pendant l’usinage et réduit également le frottement et la formation de copeaux ‒ quand la contrainte opposée par les fortes forces de coupe provoquent la déformation du plastique sur le logement de plaquettes. Grâce à cette propriété, le siège de pointe reste sécurisé et ne se déforme pas, ce qui prolonge la durée de vie de l’outil.
Ensuite, cela offre une autre solution que le concept des quatre bords évoqués plus haut : le CoroMill® MH20 est conçu avec une plaquette à deux bords. Avec ce concept des deux bords, lors de l’usinage contre des épaulements ou dans des angles, l’autre arête des plaquettes est protégée et pourra offrir des performances égales lors de l’indexage. Les avantages sont une plus grande fiabilité et une meilleure protection contre l’usure. La ligne d’arête du principal bord coupant de la plaquette et le rayon d’angle sont aussi optimisés pour une plus grande sécurité de process.
La géométrie des arêtes de coupe de la fraise CoroMill® MH20 est une autre spécificité innovante. De plus, Sandvik Coromant introduit pour la première fois avec les concepts de fraisage grande avance des géométries de plaquettes spécifiques adaptées à différents groupes de matières ISO afin d’offrir plus de sécurité des process et plus de productivité. Avec le CoroMill® MH20, la conception inclinée de l’arête offre une action coupante graduelle et légère, qui consomme moins d’électricité, donc adaptée à l’utilisation de machines plus petites.
Les CoroMill® MH20 de Sandvik Coromant s’est révélé remarquablement plus résistant au temps que les outils de générations précédentes ‒ jusqu’à 30 % de durée de vie en plus dans certains cas, bien que cette performance diffère en fonction des matériaux.
Usinage de précision
Un client de Sandvik Coromant, un gros atelier canadien spécialisé dans l’usinage de moules, souhaitait améliorer son outillage. Ce client utilisait l’outil d’un concurrent, qui souffrait des vibrations qui rendaient les process d’usinage imprévisibles et peu sûrs.
Pour résoudre ce problème, l’atelier s’est tourné vers Sandvik Coromant pour tester la performance du CoroMill® MH20 par rapport à son outil précédent. Les deux outils ont été utilisés pour réaliser des usinages de poches compliqués sur des pièces en H13, un acier au chrome prisé pour le travail à chaud, connu pour sa haute rigidité et sa forte résistance à la fatigue, pour produire un moule.
Chaque outil de fraisage mesurait 25.4 mm (1 po.) et tournait à une vitesse de coupe (vc) de 168 m/min (550 pi./min). Le CoroMill® MH20 était utilisé à un taux légèrement supérieur d’avance rapide avec deux plaquettes, car cela permettait d’augmenter la profondeur de coupe de 35 %. Les paramètres étaient les suivants : une avance par dent (fz) de 1 mm/dent (0.04 po./dent), une vitesse d’avance (vf) de 5 080 mm/min (200 po./min) et une profondeur de coupe axiale (ap) de 0.8 mm (0.031 po.).
L’outil concurrent était utilisé à une fz de 0.63 mm/dent (0.025 po./dent), vf de 4 572 mm/min (180 po./mm) et ap de 0.5 mm (0.020 po.). Les deux outils ont été utilisés jusqu’à ce qu’ils montrent des signes d’usure en dépouille.
Malgré les paramètres de coupe plus exigeants, le CoroMill® MH20 a terminé un composant entier sans indexage, et avec une meilleure finition de surface. Il a révélé une augmentation de la durée de vie de 50 % en fonctionnant pendant 300 min., avec une réduction de la durée de cycle de 50 %. L’outil concurrent, en revanche, a fonctionné pendant la moitié du temps, soit 150 min. Il a nécessité un indexage de plus en raison de sa mauvaise durée de vie, qui, en plus, a augmenté la durée des cycles. Comme dit précédemment, la plaquette du concurrent a souffert des vibrations qui ont desserré les vis pendant l’usinage.
En passant au CoroMill® MH20, ce client a bénéficié d’une durée de vie d’outil nettement plus longue et de process d’usinage plus sûrs et sans vibrations. Même si, comme l’observe PwC, la perturbation est la seule constante dans le monde de l’usinage industriel d’aujourd’hui, les innovations d’outillage telles que le CoroMill® MH20 offrent une plus longue durée de vie et une plus grande sécurité des process. Un énorme avantage pour la compétitivité des fabricants.
BIG KAISER élargit son offre de barres d’alésage Smart Damper pour les tours
Avec son diamètre de 60 mm et sa longueur de 520 mm, le nouveau modèle ST50-SDB60DP-520 est le plus grand de la série. Il vient s’ajouter aux versions 40 mm et 32 mm déjà disponibles chez BIG KAISER. Ces barres d’alésage conviennent pour tous les marchés utilisant des tours avec interfaces cylindriques. Le mécanisme Smart Damper absorbe les vibrations […]
BIG KAISER annonce une version grande longueur et à rigidité élevée des fraises à plaquettes réversibles Fullcut Mill
Comparativement aux fraises à queue classiques, les outils FCM atteignent une qualité de fraisage supérieure, tout en étant par ailleurs plus économiques du fait de leurs plaquettes réversibles. Les nouveaux outils FCM sont disponibles dans les versions BBT, HSK et à queue cylindrique.Pour une stabilité maximale, les outils doivent être les plus courts possible. Plus […]
Percer l’aluminium sans dépôts
Pour usiner l’aluminium, les utilisateurs recourent plutôt à des outils spéciaux en raison d’exigences souvent très spécifiques. Mais le fabricant d’outils de haute qualité Walter présente les avantages que peut toutefois présenter un foret standard, avec le nouveau foret DC166 Supreme. Ce foret en carbure monobloc à lubrification interne a été développé spécialement pour l’usinage […]