Impression de pièces tribologiques résistantes aux agents chimiques avec le nouveau matériau FSL igus
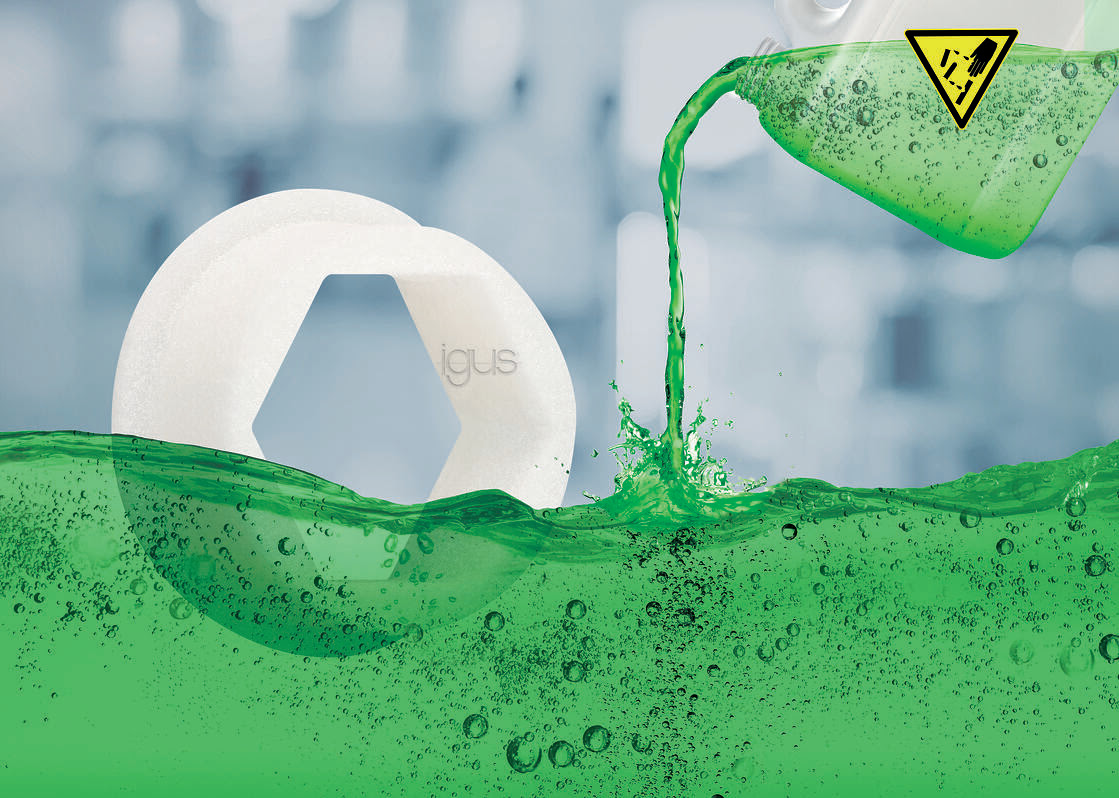
La résistance aux acides, aux bases, aux alcools, aux graisses et aux huiles n’est pas le seul avantage du matériau pour l’impression FSL iglidur I10. Il offre également une faible absorption d’humidité, une grande ténacité et aussi une grande ductilité, c’est-à-dire la capacité à se déformer plastiquement sans se rompre en présence de cisaillements. L’iglidur I10 est donc le matériau idéal pour les pièces fonctionnelles industrielles légères aux propriétés élastiques.
Sécurité alimentaire élevée : le nouveau matériau FSL est conforme aux exigences du FDA
Les applications ne manquent pas pour ce nouveau matériau. L’iglidur I10 trouvera sûrement sa place dans le secteur de la galvanisation. Les pièces imprimées qui se trouvent dans les bains électrolytiques destinés aux opérations de revêtement doivent en effet être résistantes aux acides. Elles risquent sinon de se détériorer voir même de provoquer des pannes des équipements. « Mais le nouveau matériau est aussi intéressant pour les applications dans le secteur des produits alimentaires, du conditionnement et de l’emballage », déclare Christophe Garnier, Responsable de la division paliers lisses iglidur chez igus France. « Nous sommes en effet l’un des rares fabricants à avoir fait certifier ce matériau pour l’impression FSL par le FDA, l’agence américaine de contrôle des aliments. » Le nouveau matériau répond également aux exigences du règlement européen 10/2011 qui atteste du caractère inoffensif de ce polymère en contact avec des produits alimentaires.
Des pièces industrielles fabriquées en quelques jours avec le service d’impression 3D
igus va aussi proposer le nouveau matériau pour son propre service d’impression 3D. Les clients peuvent charger en ligne un fichier STEP avec le modèle 3D de la pièce souhaitée, déterminer la quantité et choisir le matériau d’impression. igus fabrique alors les pièces sans graisse et sans entretien sur des imprimantes 3D dédiées au frittage sélectif par laser. Un laser met en fusion de très fines couches de poudre du matériau sur une plateforme qui s’abaisse couche après couche. La pièce se forme donc peu à peu. « L’avantage de ce procédé réside dans le fait qu’il n’a pas besoin de moule, ce qui est nettement plus économique et plus rapide qu’avec les méthodes classiques comme le moulage par injection, en particulier pour les prototypes et les petites séries », explique Christophe Garnier. En règle générale, le client reçoit sa pièce imprimée en iglidur I10 cinq jours après la réception de la commande.
uvex lance la teinte CBR23 : une nouvelle teinte solaire pour un effet anti-fatigue
Une teinte qui protège contre l’éblouissement tout en améliorant le confort visuel Certifiée EN 172 (filtre de protection solaire pour usage industriel), la teinte CBR23 assure une protection optimale contre l’éblouissement avec 23% de transmission. Celle-ci offre le même niveau de protection contre l’éblouissement qu’une teinte classique gris solaire mais elle est plus agréable à porter. En effet, elle accentue […]
Elargissement de la gamme des accouplements rigides courts
De nombreuses applications servo-commandées dans des secteurs tels que les semi-conducteurs, l’industrie des produits pharmaceutiques, l’emballage et la robotique nécessitent un accouplement dont les besoins en termes de couple et de rigidité en torsion dépassent la capacité d’un accouplement flexible. Bien qu’un accouplement rigide traditionnel réponde aux exigences de performances, les prérequis en matière d’encombrements […]
MolyWorks rationalise sa production
3D Systems (NYSE:DDD) a annoncé que MolyWorks, une entreprise californienne spécialisée dans l’économie circulaire du métal, a intégré la DMP Flex 350 à son flux de production. Ceci lui a permis d’améliorer considérablement son processus de production, notamment en termes de rendement, et d’étendre ses capacités en fournissant à ses clients des pièces d’utilisation finale fabriquées […]