Spare Parts 3D se prépare à révolutionner l’adoption de l’impression 3D
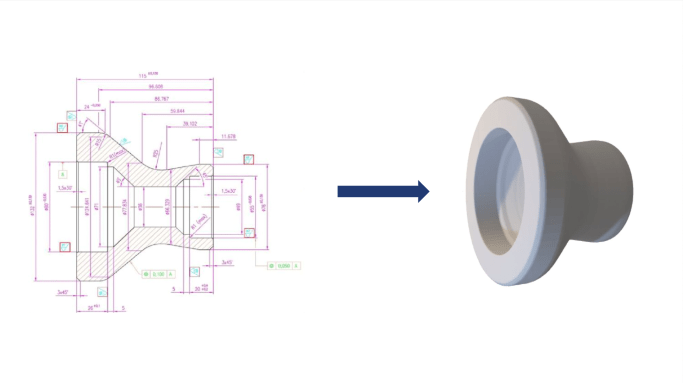
SP3D édite DIgiPART, un logiciel (basé sur du machine learning) qui permet aux industriels de déterminer efficacement quelles pièces détachées ont une solution d’impression 3D, un cas économique positif. Le logiciel permet ensuite la création d’un inventaire digital dynamique prêt pour l’impression 3D. La spécificité de DigiPART est de réaliser cette analyse technique avec des données partielles notamment sans avoir systématiquement un modèle 3D. Les algorithmes complexes de DigiPART permettent de combiner la reconnaissance sémantique, la lecture de plans 2D, avec les bases de données du matériau et processus de fabrication additive. C’est ce qui permet à la solution DigiPART d’être automatisée, précise et transparente.
Rappelons que l’objectif de ce processus d’identification est de simplifier et décarboner la chaîne d’approvisionnement de pièces détachées industrielles en les produisant à la demande et à l’endroit où elles sont nécessaires.
L’un des principaux freins à la pleine adoption de la 3D est la disponibilité de modèles 3D des pièces d’équipement industriels. Aujourd’hui, l’immense majorité des pièces est représentée sous forme de dessins techniques. Ceux-ci doivent être traités par un(e) ingénieur(e) pour être reconstruits sous forme d’un modèle 3D. Il faut en moyenne une journée pour effectuer cette tâche.
Si une entreprise, comme celles avec lesquelles SP3D travaille aujourd’hui, a un inventaire de 400 000 pièces, que 10% de ses pièces sont potentiellement imprimables en 3D, il faudrait 181 ans à un ingénieur pour reconstituer les modèles 3D !
Grâce au programme RAPID, SP3D va franchir une étape décisive dans l’automatisation du processus pour reconstruire un modèle 3D en combinant des techniques de deep leaning et de computer vision avec les technologies existantes de reconnaissance sémantique et d’OCR (d’Optical Character Recognition). Les dessins 2D regorgent d’informations ; l’objectif de SP3D est de développer l’application qui va permettre de reconstituer automatiquement un fichier 3D exploitable pour l’impression 3D.
Selon l’AID : « le projet porté par SP3D est un projet essentiel qui va permettre de débloquer l’utilisation de l’impression 3D et démultiplier ses applications dans le civil mais aussi pour la maintenance de nos équipements militaires. »
L’un des atouts de ce programme est le partenariat avec le LURPA. Ce laboratoire est un acteur majeur sur les travaux de spécification, de réalisation et de vérification géométrique des produits dans des environnements cyber-physiques de production. Grâce à l’engagement et la supervision du Dr. Charyar Mehdi-Souzani et du Pr. Nabil Anwer, respectivement coordinateur du projet et directeur adjoint du LURPA, SP3D peut compter sur une grande expertise en matière d’acquisition et de traitement géométrique de formes complexes, de rétro-conception et de reconstruction 3D, et de spécification géométrique des produits (à la base des informations reportées sur les dessins techniques)
Selon Nabil Anwer, directeur adjoint du LURPA : « la reconstruction rapide de modèles 3D à partir de dessins techniques est un vrai challenge pour lequel la combinaison de techniques de traitement numérique de la géométrie, de règles expertes et d’apprentissage profond vont permettre une avancée considérable pour la création d’inventaires numériques de produits »
Demain, un industriel utilisant DigiPART, pourra, avec simplement une description de pièce, et un plan 2D, déterminer l’existence d’une solution de fabrication additive, son coût, reconstituer son modèle 3D et la faire imprimer à la demande, à côté de son lieu d’utilisation. Le tout en quelques minutes.
Selon Christophe Migliorini, Directeur Technique (CTO) de SP3D : « Grâce à ce programme, nous avons mis en place une équipe en pointe sur ces sujets pour le développement de cette brique technologique fondamentale. Ceci va renforcer l’attractivité de notre solution DigiPART et consolider notre leadership en matière d’identification de pièces pour la fabrication additive. »
MolyWorks rationalise sa production
3D Systems (NYSE:DDD) a annoncé que MolyWorks, une entreprise californienne spécialisée dans l’économie circulaire du métal, a intégré la DMP Flex 350 à son flux de production. Ceci lui a permis d’améliorer considérablement son processus de production, notamment en termes de rendement, et d’étendre ses capacités en fournissant à ses clients des pièces d’utilisation finale fabriquées […]
Un palier lisse polymère moulé par injection en 7 jours seulement
Le problème, les ingénieurs et les responsables achats des équipementiers automobiles le connaissent bien : Se procurer le plus rapidement possible une pièce spéciale non disponible sur catalogue, un palier lisse pour le réglage en hauteur d’un siège de voiture par exemple. Alors que faire ? Lancer l’imprimante 3D ? Le palier serait certes vite imprimé mais […]
AddUp célèbre l’inauguration de sa nouvelle usine de fabrication additive
Installé au sein de la « WBA Tooling Academy » d’Aix-la-Chapelle, en Allemagne, le « Tooling Competence Centre » (Centre de Compétences AddUp dédié à l’Outillage) est un atelier de Fabrication Additive métallique, axé sur le développement d’applications dans l’industrie de l’outillage. Equipé d’une machine FormUp® 350 utilisant la technologie de fusion sur lit de poudre (PBF : « Powder Bed […]