Un vent nouveau souffle sur le fraisage trochoïdal
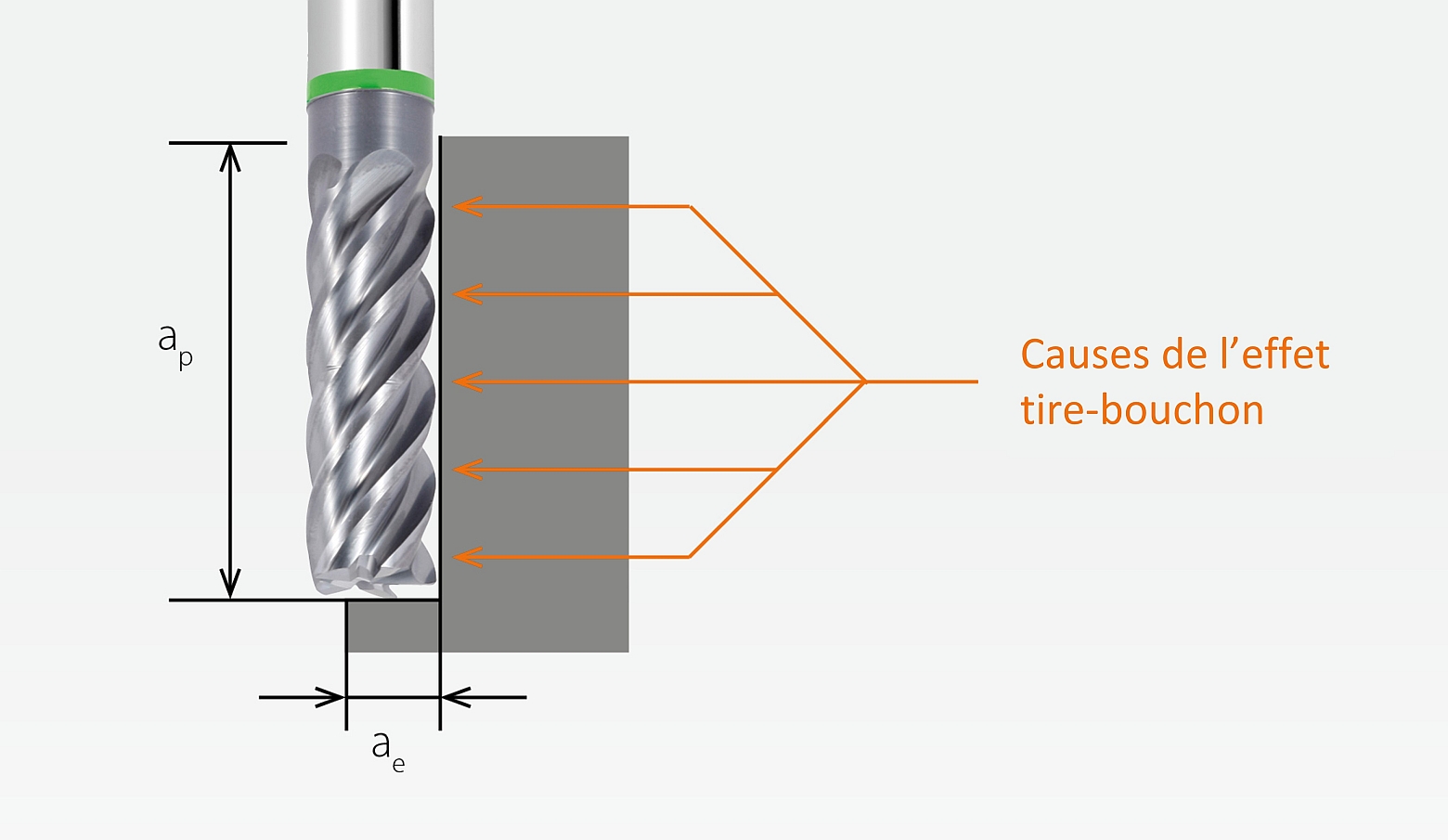
Le procédé d’usinage « fraisage trochoïdal » existe déjà depuis plus de dix ans. A une époque d’automatisation croissante en raison de la pénurie criante de main-d’œuvre qualifiée, le fraisage trochoïdal fait aujourd’hui l’objet d’un regain d’attention, car il offre une sécurité de processus élevée. Lors du fraisage TPC, l’outil se déplace en petits cercles elliptiques le long d’une ligne de bordure. Un puissant logiciel de CAO/FAO recalcule alors en permanence la trajectoire de fraisage. Même des formes complexes peuvent être fraisées à grande vitesse sur toute la profondeur de coupe. Dans le même temps, les efforts de coupe appliqués sont plus faibles qu’avec le fraisage traditionnel. L’outil est ainsi sollicité de manière plus régulière et sa durée de vie augmente.
L’outil adapté à chaque application
Les usineurs expérimentés le savent : le fraisage trochoïdal est possible avec presque tous les outils. Il est même possible d’utiliser une fraise HPC classique. Il ne s’agit toutefois pas toujours de la solution la plus économique. Pourquoi ? D’abord parce que son substrat est optimisé pour une usure élevée. Il est dur, mais moins tenace. Ensuite, les fraises classiques possèdent moins de dents et davantage de goujures en raison de l’approche. Enfin, elles ne sont souvent pas assez stables pour une utilisation TPC. En d’autres termes, une fraise classique ne peut être utilisée pour le fraisage TPC que si la vitesse d’usinage est réduite.
Il en va autrement avec les outils spécialement conçus pour le fraisage trochoïdal : ils sont optimisés pour une utilisation avec une approche latérale plus faible et un risque de rupture par flexion moindre. Ils sont fabriqués dans un substrat très tenace qui permet de très longs porte-à-faux. Les fraises TPC nécessitent en outre moins de goujures et possèdent donc plus de dents. Elles sont également plus longues (jusqu’à 5xD) et peuvent par conséquent atteindre des profondeurs de coupe plus importantes. Pour les processus de fraisage complexes avec un volume de copeaux important, il est recommandé d’utiliser des outils TPC avec un plus grand nombre de brise-copeaux. La fraise TPC GARANT Master INOX est, par exemple, fabriquée dans un substrat en carbure monobloc optimisé et se montre extrêmement résistante à la rupture par flexion, même lors de l’usinage d’aciers inoxydables et de duplex. Grâce à un diamètre d’âme renforcé, l’outil bénéficie de la rigidité nécessaire à l’usinage TPC. La géométrie de coupe se compose de six dents, d’arêtes de coupe préparées de manière ciblée et d’un plus grand nombre de brise-copeaux qui enroulent et évacuent en toute sécurité les copeaux particulièrement courts dans les goujures, ce qui augmente la sécurité des processus.
Productivité quadruplée lors de tests d’outils
Pour utiliser le procédé TPC, il est indispensable d’utiliser un puissant logiciel de CAO/FAO. Celui-ci doit recalculer en permanence la trajectoire de fraisage optimale le long de laquelle l’outil fraise les contours de la pièce. La seconde condition à remplir concerne la stabilité de serrage de la pièce et de l’outil. Le porte-outils doit donc être également doté d’une sécurité d’extraction afin que les forces axiales ne puissent pas éjecter l’outil. « L’effet tire-bouchon », qui peut se produire en cas d’accroissement de l’approche en raison de l’augmentation des points de contact entre l’outil et la pièce, est ainsi empêché.
Si ces deux conditions sont remplies, la méthode de fraisage trochoïdal avec un outil TPC peut faire valoir tous ses avantages : sécurité de processus élevée et temps de production réduit. Cela s’accompagne souvent d’une diminution des rebuts et donc d’une réduction des coûts unitaires.
Un test d’outil souligne les avantages du procédé TPC : au cours de ce test, des cavités profondes, en l’occurrence des rainures, ont été fraisées dans le matériau difficile à usiner 1.4571. Les rainures avaient une largeur de 10 mm de large et une profondeur de 40 mm.
Au premier passage, une fraise HPC classique d’un diamètre de 8 mm et d’une longueur de coupe de 21 mm a été utilisée. Les réglages suivants avaient été effectués sur la machine : Vc= 100 m/min (3 900 tr/min), fz= 0,03, ae= 1xD et ap= 1xD, ce qui résulte en 4 approches. Au final, 30 rainures ont pu être réalisées avec une sécurité de processus relativement faible.
Le même matériau a été utilisé pour le second passage avec une fraise TPC de 8 mm de diamètre et une longueur 5xD, et en appliquant la méthode de fraisage trochoïdal. Les réglages suivants avaient été effectués sur la machine : Vc= 200 m/min (8 000 tr/min), hmax= 0,2, fz= 0,739, ae=0,15 mm et ap= 39,5, avec une surépaisseur de 0,5 mm au fond pour la finition. Au final, 120 rainures ont été fraisées avec une sécurité de processus élevée.
Le test d’outil montre que la méthode de fraisage trochoïdal associée à un outil TPC parfaitement adapté au matériau à usiner peut quadrupler la productivité.
Usinage sûr de pièces de faible épaisseur
L’augmentation de la productivité obtenue avec la méthode de fraisage trochoïdal est due au fait que l’épaisseur de copeaux maximale (hmax) est figée et que l’angle d’engagement est limité, ce qui permet de fraiser avec toute la longueur de l’outil. Ceci est important, car dans le cas de pièces à contours intérieurs ou étroits, l’angle d’engagement pourrait sinon passer rapidement de 5 ou 10 degrés à 115 degrés voire plus.
La réduction de l’effort nécessaire au fraisage TPC rend l’usinage de pièces de faible épaisseur et instables plus sûr, ce qui constitue un avantage pour la pièce et l’outil. En outre, l’apport de chaleur pendant toute la durée du processus d’usinage est plus faible qu’avec les procédés de fraisage traditionnels, ce qui a des effets positifs sur les étapes de travail en aval.
C’est pourquoi le fraisage trochoïdal est principalement utilisé lorsque des matériaux très durs doivent être usinés, comme dans la fabrication d’outils et de moules, la construction métallique, mais aussi la fabrication en sous-traitance ou la construction mécanique. Cependant, même dans des environnements automatisés, ce procédé est de plus en plus utilisé en raison de son excellente sécurité des processus. La nouvelle fraise carbure monobloc TPC GARANT Master INOX a, par exemple, montré une très grande sécurité des processus en fonctionnement continu dans les aciers inoxydables et le duplex lors de tests internes.
Conclusion
Les entreprises qui souhaitent usiner efficacement des matériaux très durs peuvent quadrupler leur productivité en utilisant la méthode de fraisage trochoïdal et un outil TPC adapté. En raison de la sécurité des processus très élevée et de la longue durée de vie des outils, le procédé TPC permet également de recourir à une commande multi-machine avec le même nombre d’ouvriers qualifiés. La sécurité de processus élevée et les longues durées de vie rendent également le procédé TPC intéressant pour une utilisation dans les environnements automatisés. C’est pourquoi les entreprises qui misent de plus en plus sur l’automatisation face à la pénurie croissante de personnel qualifié et du vieillissement de la main-d’œuvre devraient, dans un avenir proche, donner un nouvel élan au procédé TPC.
BIG KAISER élargit son offre de barres d’alésage Smart Damper pour les tours
Avec son diamètre de 60 mm et sa longueur de 520 mm, le nouveau modèle ST50-SDB60DP-520 est le plus grand de la série. Il vient s’ajouter aux versions 40 mm et 32 mm déjà disponibles chez BIG KAISER. Ces barres d’alésage conviennent pour tous les marchés utilisant des tours avec interfaces cylindriques. Le mécanisme Smart Damper absorbe les vibrations […]
La robotique d’ABB au service du groupe Renault
ABB soutient le Groupe Renault en lui fournissant une technologie robotique de pointe pour l’aider à automatiser le réseau de production du fabricant de véhicules électriques sur plusieurs marchés clés. ABB a livré la majorité des 160 unités du portefeuille de grands robots industriels au cours des 24 derniers mois. Les détails financiers de la […]
BIG KAISER annonce une version grande longueur et à rigidité élevée des fraises à plaquettes réversibles Fullcut Mill
Comparativement aux fraises à queue classiques, les outils FCM atteignent une qualité de fraisage supérieure, tout en étant par ailleurs plus économiques du fait de leurs plaquettes réversibles. Les nouveaux outils FCM sont disponibles dans les versions BBT, HSK et à queue cylindrique.Pour une stabilité maximale, les outils doivent être les plus courts possible. Plus […]