Les technologies de Comau choisies par ACC pour la Gigafactory française
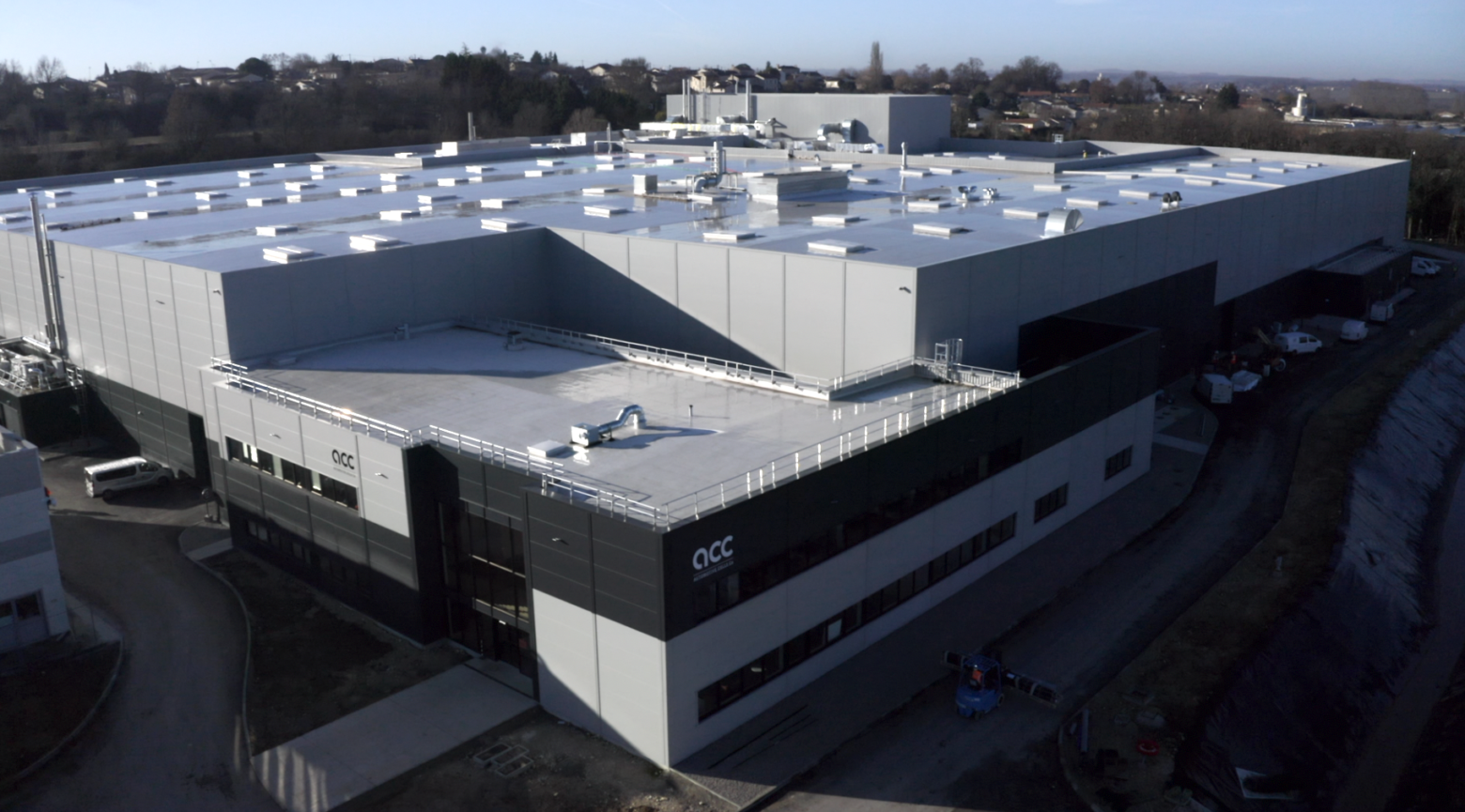
- Comau a été sélectionné par la société Automotive Cells Company (ACC), joint-venture entre Stellantis, TotalEnergies/Saft et Mercedes-Benz, pour concevoir et mettre au point une chaîne de production extrêmement intégrée de modules de batteries, destinée à sa future « giga-usine » à Billy-Bercalu Douvrain, dans le nord de la France. ACC prévoit d’atteindre progressivement 40 GWh, elle est donc en bonne place pour devenir un leader européen de la mobilité efficace et plus propre pour tous. Conformément aux termes de l’accord, Comau fournira à ACC l’expertise et l’équipement nécessaires pour automatiser la fabrication des batteries de nouvelle génération de véhicules électriques. Grâce à leur flexibilité, essentielle à la gestion des modules à huit et seize éléments, les chaînes conçues par Comau permettront à ACC de produire jusqu’à huit gigawatts-heures (GWh) par an d’ici à la fin de l’année 2024. En outre, la solution complète tire profit du vaste réseau européen de Comau, garantissant ainsi l’approvisionnement local en technologie, matériel auxiliaire et composants des cinq chaînes de fabrication, dont trois produisent les deux modèles, tandis que deux sont des chaînes réservées aux MEB à huit éléments.
Le projet se caractérise notamment par l’emploi obligatoire d’une force d’empilage de 300 à 500 décanewtons pour produire les deux formats de module, alors que la moyenne de l’industrie est d’environ 100 décanewtons. Pour relever ce défi, les ingénieurs de Comau et d’ACC ont travaillé en tandem à l’adaptation du processus, afin de garantir la géométrie et les caractéristiques de la batterie souhaitées. Cette démarche d’ingénierie simultanée a également permis à Comau de supprimer l’une des chaînes conçues à l’origine, ce qui a amélioré la dynamique des processus et aidé ACC à optimiser son investissement.
Ce projet, qui souligne l’investissement continu de Comau dans le domaine de l’électrification, tire également parti des plus de 45 ans d’expertise de l’entreprise dans les technologies d’automatisation et de numérisation. En effet, Comau a fourni à ACC la technologie et le savoir-faire nécessaires pour automatiser de bout en bout le processus de production, qui comprend la préparation et les essais des éléments prismatiques, l’empilage, le soudage et l’assemblage final, jusqu’au test en fin de chaîne. L’installation complète, qui intègre des produits propres à Comau et des produits tiers, applique le procédé d’empilage innovant de Comau, en plus de ses technologies de soudage, emballage et essais électriques.
Dans un premier temps, l’équipe d’ingénierie commune mettra en place et optimisera la chaîne pilote dans l’usine ACC de Nersac, en France, puis elle déploiera la chaîne de production à grande échelle dans la giga-usine de Billy-Bercalu Douvrain. Avec une cadence de production estimée à 53 pièces par heure, la solution conçue par Comau répond aux objectifs de fabrication à court terme du client tout en offrant la possibilité d’un agrandissement si nécessaire.
« L’émergence d’un secteur européen de l’équipement est un facteur clé de succès pour ACC, dont l’ambition est d’être un leader européen dans le domaine des éléments et des modules de batteries automobiles. En Europe, nous ne pouvons pas dépendre exclusivement d’un approvisionnement asiatique. Nous devons faciliter la constitution d’un écosystème complet de batteries, couvrant l’ensemble de la chaîne de valeur. Dans cette perspective, il est très important pour ACC de pouvoir compter sur Comau. Tout au long du projet, l’équipe d’ingénieurs de Comau a tout fait pour que nous réussissions, en améliorant à la fois la conception de nos processus et l’optimisation continue de l’équipement provenant de Comau comme d’autres fabricants », déclare Jean-Baptiste Pernot, responsable des opérations d’ACC.
« Grâce à la solide collaboration et aux compétences de nos équipes communes d’ingénierie, Comau, en tant que partenaire du développement, aide ACC à devenir un acteur de premier plan dans le domaine de la technologie des batteries haute performance », déclare Pietro Gorlier, P.-D.G. de Comau. « Ensemble, nous avons réalisé avec succès la première phase du programme de production de batteries d’ACC et nous avons hâte d’améliorer ses chaînes de production sur grande échelle au cours des prochains mois. »
BIG KAISER élargit son offre de barres d’alésage Smart Damper pour les tours
Avec son diamètre de 60 mm et sa longueur de 520 mm, le nouveau modèle ST50-SDB60DP-520 est le plus grand de la série. Il vient s’ajouter aux versions 40 mm et 32 mm déjà disponibles chez BIG KAISER. Ces barres d’alésage conviennent pour tous les marchés utilisant des tours avec interfaces cylindriques. Le mécanisme Smart Damper absorbe les vibrations […]
SPAX automatise un entrepôt de 30 000 m2 avec STILL
Sur une surface au sol de près de trois hectares, STILL et l’exploitant Rhenus Warehousing Solutions mettent en œuvre un concept intralogistique global composé de chariots de magasinage de série sans conducteur, de robots mobiles autonomes et d’un système de rayonnages VNA (allées étroites) entièrement automatisé avec plus de 42 000 emplacements de stockage. C’est […]
MolyWorks rationalise sa production
3D Systems (NYSE:DDD) a annoncé que MolyWorks, une entreprise californienne spécialisée dans l’économie circulaire du métal, a intégré la DMP Flex 350 à son flux de production. Ceci lui a permis d’améliorer considérablement son processus de production, notamment en termes de rendement, et d’étendre ses capacités en fournissant à ses clients des pièces d’utilisation finale fabriquées […]