De la valeur ajoutée grâce à des solutions modulaires
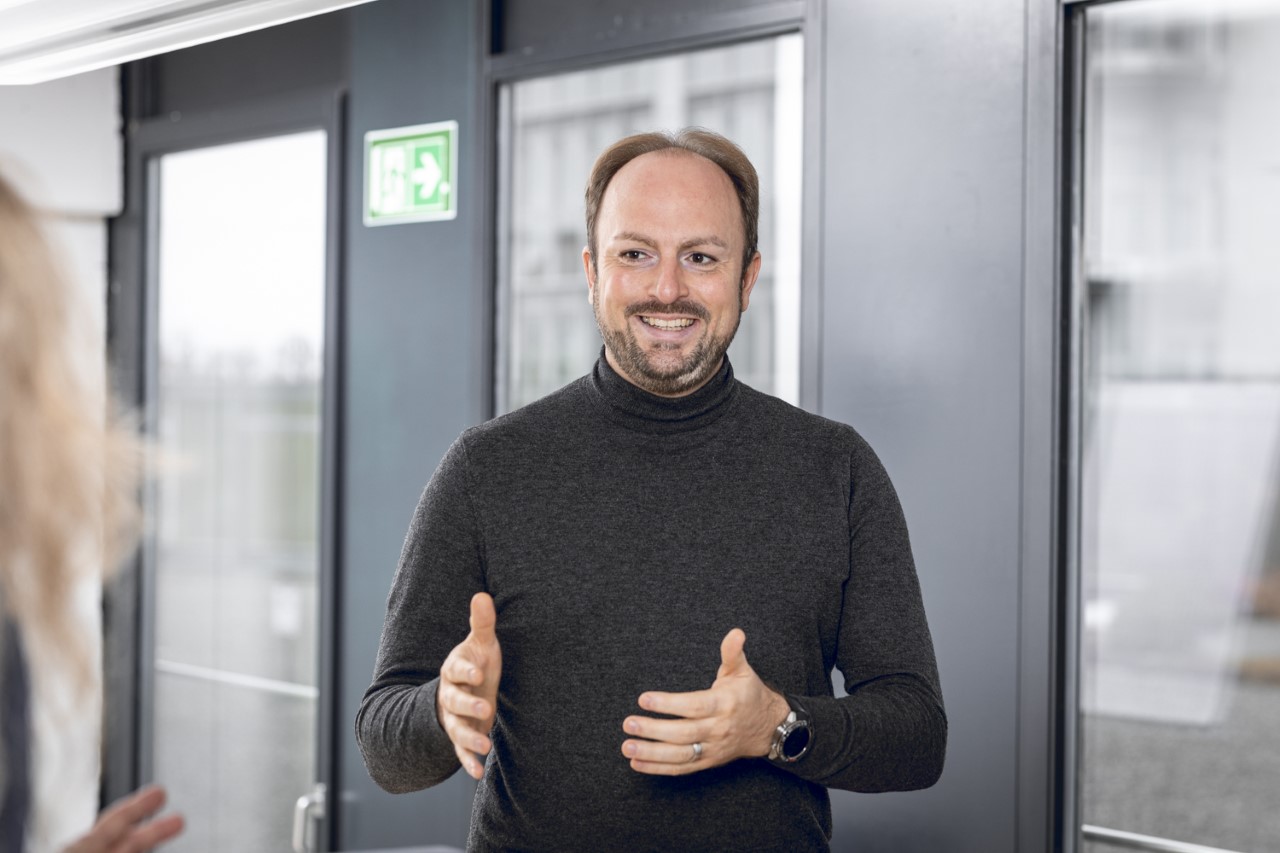
Monsieur Mayr, vous dirigez le département Fabrication numérique de Hoffmann Group depuis le printemps 2021. Qu’est-ce qui vous attire le plus dans cette fonction ?
Hoffmann Group est un distributeur d’outils, d’équipements d’atelier et d’équipements de protection individuelle. Dans son travail quotidien, notre service externe est amené à échanger avec les petites et moyennes entreprises dans le cadre d’un partenariat. Par conséquent, nous sommes largement conscients des défis qui se posent dans les entreprises manufacturières. Depuis un certain temps, nous constatons que les entreprises souhaitent digitaliser leur fabrication pour diverses raisons. C’est pourquoi nous avons commencé à travailler sur des solutions numériques appropriées. Bien sûr, il s’agit également d’un terrain inconnu pour nous, car jusqu’à présent, nous n’étions pas aussi actifs dans le développement, la mise à disposition et la prise en charge de solutions numériques. Jouer un rôle moteur dans la conception et la mise en œuvre de cette nouvelle offre de services, grâce à laquelle nous voulons que les PME continuent à réussir à l’avenir, revêt un caractère particulier pour moi.
Quels sont les défis actuels auxquels sont confrontées les entreprises manufacturières de taille moyenne en particulier ?
J’y vois essentiellement deux aspects : bon nombre d’entre elles, malgré la crise du coronavirus, tournent à plein régime. Elles veulent augmenter leur production sans réaliser d’autres investissements. Dans ce contexte, la pression sur les coûts reste un critère très important et une grande efficacité est tout simplement exigée par le marché. A cela s’ajoute une pénurie croissante de main-d’œuvre qualifiée. De nombreuses entreprises doivent de plus en plus recourir à du personnel non qualifié. Des processus digitalisés continus sont nécessaires si l’on ne veut pas mettre en péril le niveau de productivité et de qualité actuel.
Quelles mesures proposez vous ?
Je pense que la situation actuelle n’est pas facile à gérer. Si la digitalisation constitue la solution, les entreprises doivent consacrer du temps et de l’énergie supplémentaires dans un environnement plus difficile. Afin de progresser dans ce domaine sans avoir à débourser des sommes excessives, il est conseillé de faire appel à une aide extérieure. Chercher et trouver des partenaires compétents qui mettent en œuvre des solutions dans les activités courantes sans trop perturber l’exploitation est certainement un critère de réussite.
Vous voulez être l’un de ces partenaires ? Comment vous positionnez-vous pour cela ?
Au cours des derniers mois, nous avons élaboré une approche que nous considérons comme très prometteuse. Il s’agit pour nous d’aller chercher chaque entreprise là où elle se trouve afin de la faire évoluer pas à pas vers un univers digitalisé, sans pour
autant la surcharger. Afin de créer les conditions nécessaires en interne, nous avons mis en place une équipe en interne chargée du développement logiciel. Outre nos collègues qui travaillent à la structure technologique, nous disposons d’une équipe intégrée composée de responsables produits, de spécialistes de l’expérience utilisateur et de conseillers en processus qui veillent à un développement orienté utilisateur. Dans les environnements hétérogènes de systèmes et de machines de nos clients, nous apprenons extrêmement vite et, dans nos show-rooms, nous avons établi des structures de fabrication telles que nous les rencontrons souvent dans les petites et moyennes entreprises. Cela nous permet d’effectuer des tests en direct sur divers appareils, machines et structures avant de déployer une solution. Outre la convivialité proprement dite, la mise en œuvre professionnelle des solutions et l’assistance offerte par la suite jouent un rôle fondamental. C’est là qu’interviennent nos conseillers en processus avec nos techniciens de service.
Vous parlez souvent de modularité dans ce contexte. Qu’entendez-vous exactement par-là ?
Chaque entreprise manufacturière a un processus de base à valeur ajoutée. Ce processus central se compose de sous-processus qui, d’une part, recèlent des problèmes de différentes tailles et, d’autre part, sont accompagnés d’infrastructures plus ou moins hétérogènes. En général, le monstre de la « digitalisation » est tout simplement écrasant lorsque le processus global doit être abordé en une seule fois. Conformément à la stratégie « diviser pour mieux régner », nous souhaitons découper les problèmes en tranches, les rendre plus compréhensibles et les aborder de manière ciblée avec l’entreprise concernée.
Comment l’utilisateur peut-il se représenter cette approche ?
Chaque tranche de projet de digitalisation doit apporter des améliorations tangibles pour l’entreprise et ses collaborateurs avant que l’on puisse passer à la mise en œuvre de la tranche suivante. De cette façon, le terrain déjà acquis est préservé et l’ensemble du processus est digitalisé pas à pas. Nous relevons ce défi par un nombre croissant de modules numériques, dont chacun apporte une contribution tangible et peut interagir avec d’autres modules au fur et à mesure de leur développement.
La modularité vise-t-elle ainsi à répondre aux diverses exigences des entreprises en atelier ?
Précisément. Chaque entreprise doit trouver sa propre stratégie et son propre rythme en matière de digitalisation. C’est pourquoi nous voulons offrir aux PME plusieurs possibilités d’accès par le biais de différents modules adaptés à leur situation individuelle. Sur ces éléments, que j’appelle les « cellules germinales de la digitalisation », l’utilisateur peut ancrer d’autres modules et les faire interagir afin d’assurer un développement continu de sa solution. Il est important de reconnaître que la digitalisation n’est pas seulement synonyme d’introduction d’un logiciel. Elle intervient dans l’environnement de travail des collaborateurs et modifie leur quotidien. Pour que les collaborateurs acceptent les nouvelles méthodes de travail et les nouveaux processus, ils doivent être initiés étape par étape et capables de reconnaître suffisamment tôt un avantage des nouveautés.
Selon votre expérience, y a-t-il des modules qui se prêtent particulièrement bien à l’initiation ?
Bien que cela doive être considéré comme spécifique à l’entreprise, nous pouvons affirmer que des bases de données d’outils bien gérées dans les systèmes de FAO sont une condition préalable importante à l’introduction d’un logiciel de gestion d’outils d’usinage. Dans ce cas, il est judicieux d’utiliser également notre « système de gestion
des ordres de fabrication », qui est inclus dans la solution « Connected Manufacturing ». Cela permet d’exploiter tout le potentiel que recèle une prise en charge numérique du processus de production. L’un de nos utilisateurs a pu réduire les temps morts d’environ 30 % grâce à notre solution Connected Manufacturing et bénéficie désormais surtout du fait que les ordres déjà créés peuvent être rechargés dans le système et sur les machines quasiment d’une simple pression sur un bouton, si nécessaire. Lors de la phase d’introduction du logiciel, il a toutefois aussi revu et épuré l’ensemble de ses processus de fabrication. Cela a pris du temps, mais s’avère aujourd’hui payant à plusieurs égards. Je considère la nouvelle solution « Connected Metrology », une solution de gestion numérique des instruments de mesure avec service de réétalonnage intégré, comme un autre bon point d’entrée pour les entreprises qui utilisent déjà notre service d’étalonnage. En fin de compte, tout dépend des conditions et des priorités respectives de l’entreprise manufacturière. Cependant, l’objectif devrait toujours être d’obtenir rapidement une valeur ajoutée tangible afin de libérer davantage d’énergie de motivation pour l’étape suivante.
Quel type de solutions numériques allons-nous voir à l’avenir sous votre égide chez Hoffmann ?
Nous avons beaucoup d’idées. Pour établir des priorités, nous travaillons largement en nous basant sur la valeur ajoutée et les données du marché. Nous observons également comment les acteurs du marché abordent le problème afin de générer la meilleure offre de solutions et de donner une orientation. L’important est d’intégrer dans notre offre actuelle de nouvelles solutions et de nouveaux services numériques de manière à créer une offre élargie avec une réelle valeur ajoutée. Nous voulons contribuer au maximum à la productivité de nos clients et occuper ainsi une position clé en tant que partenaire dans les entreprises manufacturières.
Un palier lisse polymère moulé par injection en 7 jours seulement
Le problème, les ingénieurs et les responsables achats des équipementiers automobiles le connaissent bien : Se procurer le plus rapidement possible une pièce spéciale non disponible sur catalogue, un palier lisse pour le réglage en hauteur d’un siège de voiture par exemple. Alors que faire ? Lancer l’imprimante 3D ? Le palier serait certes vite imprimé mais […]
Adaptateurs et raccords pour les applications haute pression
Les adaptateurs HPAC permettent une connexion sûre aux vannes, aux embouts et aux raccords, même dans des situations d’installation confinées, comme dans les bancs d’essai et les armoires de commande.Ils sont disponibles dans toutes les variantes courantes (femelle- mâle, mâle-mâle, femelle-femelle) et avec un filetage NPT ou une combinaison cône-filetage (C&T).La construction monobloc et les […]
Colles de haute technologie pour les cellules solaires à couches minces
Les cellules photo-actives à couches minces sont utilisées pour les façades, les toits légers ou les bornes de recharge. Elles sont constituées de plusieurs couches d’une épaisseur de l’ordre du millimètre. Les couches actives, productrices d’énergie, sont souvent déposées en phase vapeur sur du verre ou un matériau porteur organique et recouvertes d’un film protecteur […]