Numérisation de l’assurance qualité dans le secteur automobile
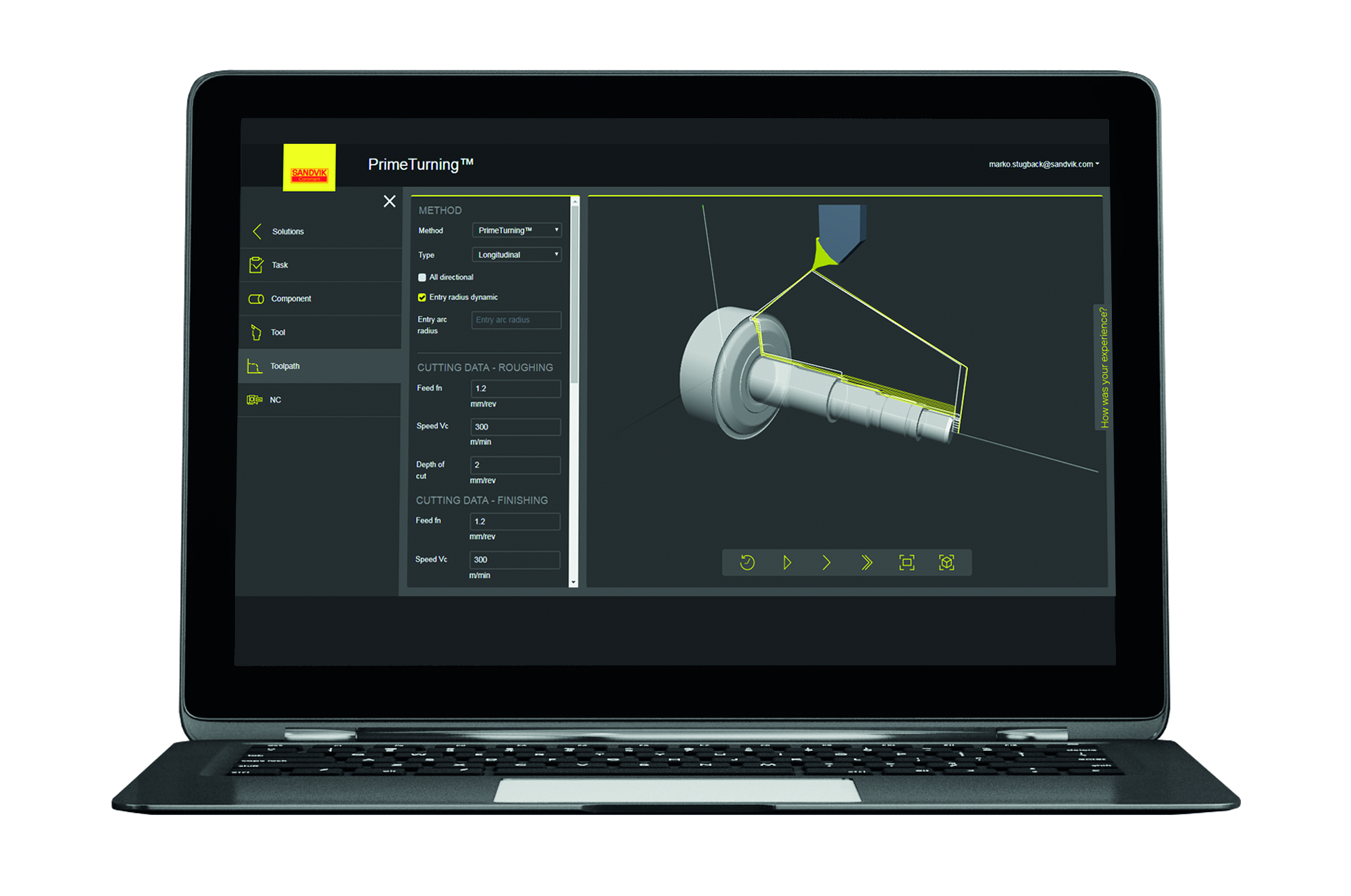
Selon le rapport Automotive 2030 — Racing toward a digital future d’IBM, la moitié des dirigeants du secteur automobile affirme que leur entreprise doit se réinventer numériquement pour réussir… ou tout simplement survivre. Il est clair que cela peut leur faire gagner en productivité et en flexibilité, en délai de mise sur le marché aussi, mais qu’en est-il de la qualité ? Jens Nannen, Digital Machining Sales Technology Manager pour l’Europe chez le leader dans le domaine de la coupe du métal Sandvik Coromant nous explique pourquoi de meilleurs systèmes de surveillance et de commande constituent une garantie de qualité et de survie pour les constructeurs automobiles.
Nombre des acteurs majeurs de l’automobile mettent en œuvre des process numériques pour améliorer leur production. Par exemple, BMW a déployé une plateforme d’Internet des objets (IoT) dans son usine de Bavière, qui propose désormais une large gamme d’outils et d’accessoires numériques que les employés de BMW peuvent combiner pour créer leurs propres solutions prêtes à l’emploi. La plateforme a ainsi permis de réduire de 80 % les délais de déploiement de nouvelles applications logicielles et de diminuer de 5 % les problèmes de qualité des pièces produites. Parallèlement, Volkswagen s’est associée à un développeur d’applications basées sur la réalité augmentée pour étiqueter ses pièces automobiles. Elle peut ainsi associer plus facilement chaque pièce au meilleur outil nécessaire pour l’usiner. L’efficacité des techniciens de service de Volkswagen s’en est trouvée considérablement accrue.
Les machines à commande numérique (CNC) et les tours d’aujourd’hui sont plus connectés que jamais. Les procédés d’usinage génèrent des caractéristiques physiques aux valeurs mesurables, et les capteurs et l’IoT permettent de surveiller les temps de fonctionnement, les temps d’arrêt et la disponibilité des machines. Ces technologies offrent également la possibilité d’identifier la cause profonde de problèmes spécifiques, comme les casses d’outils et de machines – qui sont parmi les causes les plus courantes d’interruption de la production. Selon l’agence de formation TPC, on estime qu’une minute de temps d’arrêt peut s’avérer extrêmement coûteuse, et qu’une heure d’interruption d’activité d’un constructeur automobile se chiffre en milliers de dollars.
Ces pertes ne sont tout simplement pas acceptables en usinage de composants automobiles. Les engrenages et les arbres d’entraînement sont généralement fabriqués en acier forgé, un alliage tout indiqué pour produire des pièces grandes et robustes, mais délicat à usiner. En effet, les matériaux forgés présentent des profondeurs irrégulières qui nécessitent des tolérances d’usinage différentes : allant de 0,5 mm à plus de 1 mm, ces fluctuations de profondeur de coupe rendent les outils plus sujets aux ruptures.
Dans le cadre de l’assurance qualité, le monitorage minutieux de l’usinage de pièces forgées et en fonte peut également s’avérer difficile. Détecter les bris d’outils sur les chaînes de production automobile n’est pas chose aisée car les modulations des conditions de coupe, les sur-épaisseurs variables ou les pièces asymétriques sont autant de facteurs connus pour déclencher de fausses alarmes. Si l’usinage en atelier n’est pas parfaitement adapté, toute déviation indésirable peut détériorer l’outil de coupe, la machine-outil ou la pièce elle-même.
Alors, que faut-il faire ? Les systèmes de surveillance plus sophistiqués, qui permettent une meilleure commande, et les systèmes IoT qui soutiennent le travail vital des opérateurs manuels sur la ligne de production, sont partie de la réponse.
Des décisions numériques
Les solutions qui surveillent les processus d’usinage en temps réel permettent aux fabricants de réagir plus rapidement aux problèmes. La technologie de contrôle des processus s’appuie sur des capteurs dont les algorithmes uniques calculent et détectent les bris d’outils en temps réel. Ainsi, en cas de problème, le système peut arrêter immédiatement l’avance et rétracter l’outil et le fabricant peut résoudre le problème avant qu’il ne se traduise en interruption de production.
Autre exemple avec la détection des collisions et des surcharges : le système surveille la force d’usinage et les vibrations pendant les cycles de production et arrête l’avance s’il détecte une éventuelle surcharge. Les collisions peuvent ainsi être résolues plus rapidement et les scénarios de rupture catastrophiques évités.
Essayons maintenant de pousser le concept de maintenance prédictive un peu plus loin. Et s’il était possible de s’assurer que les trajectoires d’outils sont correctes avant de commencer l’usinage pour améliorer le résultat final et limiter les risques de ruptures ?
Le logiciel CoroPlus® Tool Path a justement été créé pour tracer des trajets d’outil spécifiques pour des méthodes d’usinage telles que le PrimeTurning™ qui augmente la productivité, la durée de vie de l’outil et la sécurité de process. Le logiciel fournit des techniques et codes de programmation pour configurer convenablement les paramètres et variables d’une application donnée (sur une ligne de production automobile, par exemple) pour garantir un rendement maximum. Hébergé dans le cloud, le logiciel est facilement accessible depuis un navigateur et ouvre la collaboration et le partage au sein de l’entreprise. Le code généré par le logiciel peut être facilement modifié et exporté vers la machine numérique. Mis ainsi à disposition des opérateurs, il contribue à accélérer les opérations et la planification des process.
Il est impossible d’éradiquer tous les problèmes et interruptions sur les chaînes de production automobile. Néanmoins, la dématérialisation s’avère cruciale pour minimiser les effets des interruptions de production tout en surmontant les défis de productivité, de coûts et de temps d’arrêt auxquels sont confrontés les fabricants. Si l’on se base sur les conclusions d’IBM, selon lesquelles 50 % des dirigeants du secteur automobile affirment que leur entreprise doit se réinventer numériquement, il semble inévitable que la transformation numérique, avec tous ses avantages, balaie tout le secteur l’industrie. Ce qui est plutôt une bonne nouvelle. Les solutions de surveillance et de contrôle des processus telles que CoroPlus® Tool Path seront au premier plan pour faire progresser l’industrie automobile dans la dématérialisation.
Sandvik Coromant
Partie intégrante du groupe mondial d’ingénierie industrielle Sandvik, Sandvik Coromant est à l’avant-garde des outils de fabrication, des solutions d’usinage et des connaissances qui déterminent les normes et les innovations exigées par l’industrie transformatrice des métaux aujourd’hui et pour la prochaine ère industrielle. Le soutien à la formation, les investissements considérables en R&D et les partenariats solides avec les clients garantissent le développement de technologies d’usinage qui changent, dirigent et orientent l’avenir de la fabrication. Sandvik Coromant détient plus de 1 700 brevets dans le monde, emploie plus de 7 700 personnes et est représentée dans 150 pays. Pour plus d’informations, visitez www.sandvik.coromant.com ou joignez-vous à la discussion sur les réseaux sociaux
Un palier lisse polymère moulé par injection en 7 jours seulement
Le problème, les ingénieurs et les responsables achats des équipementiers automobiles le connaissent bien : Se procurer le plus rapidement possible une pièce spéciale non disponible sur catalogue, un palier lisse pour le réglage en hauteur d’un siège de voiture par exemple. Alors que faire ? Lancer l’imprimante 3D ? Le palier serait certes vite imprimé mais […]
Adaptateurs et raccords pour les applications haute pression
Les adaptateurs HPAC permettent une connexion sûre aux vannes, aux embouts et aux raccords, même dans des situations d’installation confinées, comme dans les bancs d’essai et les armoires de commande.Ils sont disponibles dans toutes les variantes courantes (femelle- mâle, mâle-mâle, femelle-femelle) et avec un filetage NPT ou une combinaison cône-filetage (C&T).La construction monobloc et les […]
Colles de haute technologie pour les cellules solaires à couches minces
Les cellules photo-actives à couches minces sont utilisées pour les façades, les toits légers ou les bornes de recharge. Elles sont constituées de plusieurs couches d’une épaisseur de l’ordre du millimètre. Les couches actives, productrices d’énergie, sont souvent déposées en phase vapeur sur du verre ou un matériau porteur organique et recouvertes d’un film protecteur […]